Discover the world of spray catalysts and learn how they contribute to enhanced surface protection, durability, and functionality in various coating applications.
Introduction
Spray catalysts are specialized materials designed to improve the performance and properties of coatings applied through spray techniques. These innovative catalysts play a crucial role in promoting better surface protection, durability, and functionality across a wide range of industries, including automotive, aerospace, marine, and construction. This article delves into the concept of spray catalysts, their applications, and the advancements that are shaping their future.
Understanding Spray Catalysts
Spray catalysts are typically composed of metal or metal oxide nanoparticles, which are integrated into the coating formulation or applied as a separate layer during the spray coating process. They function by facilitating chemical reactions that help to enhance the cross-linking, curing, and adhesion of the coating, resulting in improved surface protection and performance.
Applications of Spray Catalysts
The versatility of spray catalysts has led to their widespread adoption across various coating applications. Some of the most prominent applications include:
Automotive: Spray catalysts are used in automotive coatings to improve the durability, scratch resistance, and appearance of vehicle surfaces. By enhancing the curing and cross-linking of the coating, these catalysts contribute to better protection against corrosion, UV radiation, and environmental contaminants.

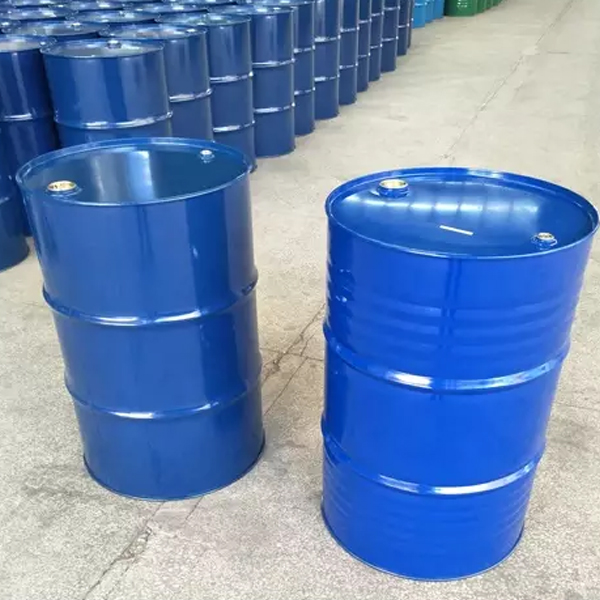
Aerospace: In the aerospace industry, spray catalysts are employed to enhance the performance of coatings applied to aircraft surfaces. These catalysts help to improve the resistance to high temperatures, humidity, and chemical exposure, ensuring the longevity and safety of aerospace components.
Marine: The marine sector benefits from spray catalysts in the form of anti-fouling and anti-corrosion coatings, which protect ships and offshore structures from the damaging effects of seawater and marine organisms. These catalysts contribute to improved coating performance and reduced maintenance requirements.
Construction: Spray catalysts are used in various construction coatings, such as anti-graffiti, waterproofing, and fire-resistant coatings. By enhancing the properties of these coatings, spray catalysts help to extend the lifespan of buildings and infrastructure while improving their overall appearance and functionality.
Advancements in Spray Catalysts Technology
The field of spray catalysts is continually evolving, with researchers and manufacturers constantly seeking to develop new and improved materials. Some of the latest advancements in spray catalysts technology include:
Nanotechnology: The integration of nanotechnology in spray catalysts has led to the creation of advanced materials with enhanced properties, such as increased surface area, improved stability, and better dispersion. These features contribute to more efficient and effective coating performance.
Eco-friendly Catalysts: In response to growing environmental concerns, the development of eco-friendly spray catalysts has gained momentum. These materials are designed to reduce volatile organic compound (VOC) emissions and minimize waste generation during the coating process.
Smart Coatings: Smart coatings, also known as responsive coatings, are a new generation of coating systems that can change their properties in response to external stimuli, such as temperature, light, or pH. Spray catalysts play a crucial role in the development of these intelligent materials.
The Future of Spray Catalysts
As the demand for high-performance, durable, and eco-friendly coatings continues to grow, the market for spray catalysts is expected to expand significantly. According to a recent study, the global spray catalysts market is projected to reach USD 2.5 billion by 2026, growing at a CAGR of 5.5% during the forecast period.
The future of spray catalysts lies in the development of advanced materials that can address the evolving needs of various industries. Researchers are focusing on creating multifunctional catalysts that can provide multiple performance benefits simultaneously, such as corrosion resistance, self-healing, and anti-microbial properties. Additionally, the development of sustainable and eco-friendly spray catalysts will continue to be a priority, as the world moves towards a greener and more environmentally conscious future.
Conclusion
Spray catalysts have undeniably transformed the landscape of coating technology, offering unparalleled surface protection, durability, and functionality. As advancements in technology continue to shape the future of spray catalysts, we can expect to see even more innovative and sustainable solutions that will further revolutionize various industries. With their unique properties and wide-ranging applications, spray catalysts are truly a testament to the power of human ingenuity and the relentless pursuit of progress.